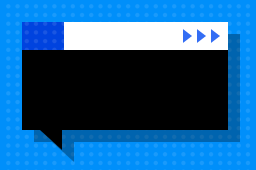
- 时间:2023-04-27 12:11:24
- 小编:zdfb
- 文件格式 DOC

在日常的学习、工作、生活中,肯定对各类范文都很熟悉吧。范文怎么写才能发挥它最大的作用呢?下面是小编帮大家整理的优质范文,仅供参考,大家一起来看看吧。
金属切削加工原理篇一
金属切削加工中产生的振动是一种十分有害的现象。若加工中产生了振动,刀具与工件间将产生相对位移,会使加工表面产生振痕,严重影响零件的表面质量和性能;工艺系统将持续承受动态交变载荷的作用,刀具极易磨损(甚至崩刃),机床连接特性受到破坏,严重时甚至使切削加工无法继续进行;振动中产生的噪音还将危害操作者的身体健康。为减小振动,有时不得不降低切削用量,使机床加工的生产效率降低。因此,分析金属切削加工中的振动原因并掌握控制振动的途径是很有必要的。
以车削加工为例。在车床安装时加设隔振地基、传动系统无缺陷以及切削过程中无冲击存在的情况下,车削振动的主要类型是不随车削速度变化而变化的自激振动(即振颤现象),其主要原因是加工过程中工件及刀架系统变形而产生的低频振动(其频率接近工件的固有频率)以及因车刀的变形而产生的高频振动(其频率接近车刀的固有频率)。这类振动常常使机床尾座、刀架松动并使硬质合金刀片碎裂,且在工件切削表面留下较细密的痕迹。车削中的低频振动通常是工件、刀架都在振动(工件振动较大),它们时而相离(振出),时而趋近(振入),产生大小相等、方向相反的作用力与反作用力(即切削力fy和弹性恢复力f弹)。刀架的振出运动是在切削力fy作用下产生的,对振动系统而言,fy是外力。在振动过程中,当工件与刀架作振出运动时,切削力f振出与工件位移方向相同,对振动系统作正功,振动系统则从切削过程中吸收一部分能量w振出储存在振动系统中;刀架的振入运动则是在弹性恢复力f弹作用下产生的。当刀架振入时,f振入与工件位移方向相反,振动系统对切削过程作功,即振动系统要消耗能量w振入。由于切削力周期性变化,使得w振出> w振入或f振出>f振入,从而使工件或刀具获得了能量补充产生低频的自激振动。此时,在力和位移的`关系图中,振出过程曲线处在振入过程曲线的上部(如图1 所示)。
图1
而高频振动产生的原因是在某速度区段内,刀具后刀面与切屑之间的摩擦,使切削力fy随切削速度v的增加而减小,即具有下降特性,造成f振出>f振入,故加工系统有自激振动产生。
自激振动与切削过程本身有关,也与工艺系统的结构性能有关。因此控制自激振动的基本途径是减少或消除激振力。控制方法有如下几个方面:
2.1 合理选择切削用量
车削加工在速度v=20~60m/min时容易产生自振,高于或低于此范围则振动减弱。因此,在精密加工时宜采用低速切削,一般加工宜采用高速切削。
进给量f增大,自振强度下降(如图2a所示)。切削宽度blim与进给量f的关系曲线见图2b,可知在允许条件下应尽量加大进给量f。车削加工时切削深度ap与切削宽度b的关系为b=ap/sinf(f为主偏角),即ap越大,切削宽度b越大,越有产生振动的趋势。
a b
图2
2.2 合理选择刀具几何参数
主要影响参数为主偏角f和前角g。如图3所示,当f=90°时振幅最小,此时切削力在y方向上最小、x方向上最大。由于一般工艺系统的刚度在x方向比y方向上好得多,因此不易起振。由图4可见,在相同切削速度v时随前角g的增大,切削力减小,振幅也减小。因此通常采用双前角消振刀(见图5)以减小切削力,可取得很好的减振效果。
a b
图3 主偏角对振动的影响
图4 前角的影响
图5 双前角消振刀
减小后角有利于减振。一般后角取2°~3°为宜,必要时在后刀面上磨出带负后角的消振棱,形成倒棱减振车刀(如图6)。其特点是刀尖不易切入金属,且后角小,有减振作用,切削时稳定性好。
图6 倒棱减振车刀
2.3 合理提高系统刚度
车削细长轴(l/d > 12)时,工件刚性差,易弯曲变形产生振动。此时应在采用弹性顶尖及辅助支承(中心架或跟刀架)来提高工件抗振性能的同时,用冷却液冷却以减小工件的热膨胀变形;当用细长刀杆进行孔加工时,应采用中间导向支承来提高刀具的抗振性能。
在增加工艺系统刚度的同时,应尽量减小构件自身的重量,应把“以最轻的质量获得最大的刚度”作为结构设计的一个重要原则。
减小刀具悬伸长度。一般情况下刀具伸出长度不宜超过刀杆高度的两倍。
使用消振器和消振刀具。如采用切向刚度较高的弹性刀杆(见图7),将不易产生刀杆的弯曲高频振动。
刀具高速自振时,宜提高转速和切削速度,以提高切削温度,消除刀具后刀面摩擦力下降特性和由此引起的自振,但切削速度不宜高于1.33m/s(80m/min)。
对机床主轴系统,要适当减小轴承间隙,滚动轴承应施加适当的预应力以增加接触刚度,提高机床的抗振性能。
合理安排刀具和工件的相对位置。在车床上安装车刀的方位对提高车削加工过程的稳定性、避免自激振动具有很大的影响。试验表明,将普通车床车刀安装在水平面上其稳定性最差,而将车刀装在a=60°的方位上,车削过程的稳定性最好。
您可能关注的文档
- 2023年中考材料作文审题立意训练题大全(大全17篇)
- 高中我国的基本经济制度教案 高中政治我国的基本政治制度教案模板
- 2023年建议书500(4篇)
- 装卸工具租赁合同四篇(通用)
- 2023年一枚小吃货作文(汇总12篇)
- 最新成长的烦恼作文开头及结尾摘抄(通用8篇)
- 2023年单位领导证婚致辞(汇总9篇)
- 最新阅读兴趣小组活动记录表(模板19篇)
- 最新巡察谈话情况报告(实用10篇)
- 2023年税务局编外人员管理情况报告(7篇)
- 学生会秘书处的职责和工作总结(专业17篇)
- 教育工作者分享故事的感悟(热门18篇)
- 学生在大学学生会秘书处的工作总结大全(15篇)
- 行政助理的自我介绍(专业19篇)
- 职业顾问的职业发展心得(精选19篇)
- 法治兴则民族兴的实用心得体会(通用15篇)
- 教师在社区团委的工作总结(模板19篇)
- 教育工作者的社区团委工作总结(优质22篇)
- 体育教练军训心得体会(优秀19篇)
- 学生军训心得体会范文(21篇)
- 青年军训第二天心得(实用18篇)
- 警察慰问春节虎年家属的慰问信(优秀18篇)
- 家属慰问春节虎年的慰问信(实用20篇)
- 公务员慰问春节虎年家属的慰问信(优质21篇)
- 植物生物学课程心得体会(专业20篇)
- 政府官员参与新冠肺炎疫情防控工作方案的重要性(汇总23篇)
- 大学生创业计划竞赛范文(18篇)
- 教育工作者行政工作安排范文(15篇)
- 编辑教学秘书的工作总结(汇总17篇)
- 学校行政人员行政工作职责大全(18篇)

